未來製造震撼彈:當AI遇上金屬3D列印,揭開金屬3D列印設計無限可能的新紀元!
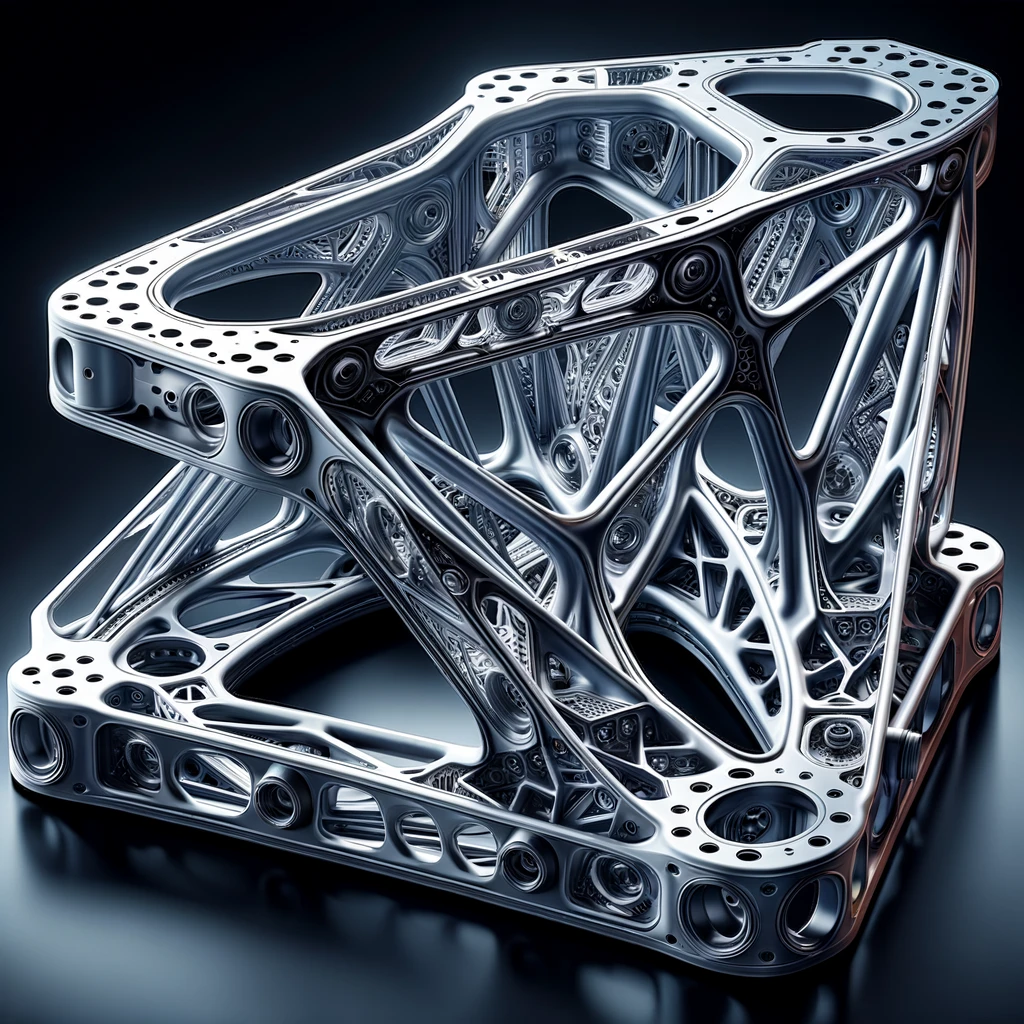
未來製造業的革命:人工智慧AI與金屬3D列印的完美融合
隨著科技的不斷進步,金屬3D列印技術在各行各業的應用日益廣泛,從航空航天到精密醫療器械,都在見證著這一技術帶來的革命性變化。然而,要充分利用金屬3D列印的潛力,遵循精確的設計規範是關鍵。這不僅要求設計師具備對材料特性和製造流程的深刻理解,還需要他們能夠在設計階段預見並解決潛在的製造問題。在這一背景下,人工智能(AI)技術的融入,為設計師提供了前所未有的支持,幫助他們突破傳統思維的束縛,探索金屬3D列印的新領域。
引言
- 簡介金屬3D列印技術的發展和應用前景。
- 強調設計規範在金屬3D列印成功實施中的重要性。
- 介紹AI如何幫助設計師遵循這些規範並開拓創新設計。
金屬3D列印的設計規範概覽
- 懸空結構與支撐策略
- 孔徑與結構形狀的優化
- 尖角與邊緣收縮的處理
- 通過具體實例說明每個規範的應用及其重要性。
金屬3D列印的設計規範概覽
金屬3D列印的成功很大程度上依賴於對懸空結構、孔徑、尖角處理及邊緣收縮等因素的精確控制。例如,適當的支撐設計可以預防結構變形,而對孔徑和結構形狀的優化則有助於提升零件的整體質量和功能性。面對這些複雜的設計要求,即使是經驗豐富的設計師也可能感到頭疼。這正是AI技術發揮作用的舞台。
AI在設計優化中的角色
AI技術能夠透過數據分析和機器學習算法,為設計師提供具體的設計改進建議。從自動識別潛在的製造問題,到提出創新的設計方案,AI在設計過程中起著不可或缺的作用。更重要的是,AI能夠引導設計師探索那些人類可能未曾想到的設計可能性,從而推動金屬3D列印技術的創新發展。
DfAM(Design for Additive Manufacturing):重塑未來製造業的雙引擎
設計適用於增材製造與ai相結合
「不以規矩,不成方圓。」針對增材製造的設計原則已經有許多先驅進行了深入的研究和明確的闡述,本章也將對一些關鍵的設計原則進行詳細描述。理解適用於增材製造的設計原則,並在設計過程中加以應用,可以簡化增材製造的生產流程以及後期處理工作。
最佳的設計不僅要考慮視覺美學,還要賦予零件額外的功能性設計,例如晶格結構、拓撲優化、隨形設計、一體化設計等。設計是靈魂所在,在這一系列賦能過程中,清晰地展現出它的重要性。如何更好地理解這些設計方法,以及如何將它們應用到零件中,接下來的章節將圍繞這些主題進行討論。
「百煉才能成鋼」,設計需要進行多次迭代,增材製造仿真在這一過程中也發揮了輔助作用。在最終生產的階段,3D列印印策略、3D列印參數以及對最終零件的成型性和質量有著重要的影響。
金屬3D列印-設計規範
1.零件擺放-從支撐進行考量
2c. 考慮支撐添加量
在增材製造中,從需要添加支撐的量來考慮,常常給出一個約45°斜角擺放的建議。這是因為在某些角度下,零件需要的支撐量最少,主要目的是為了避免後期移除支撐時的問題以及在金屬3D列印過程中能夠節省時間和成本。
2d. 內部支撐添加角度
從內部支撐添加的角度來看,許多時候這個選擇比較複雜,因為內部支撐難以移除或者無法移除。在擺放零件時,很多精力會花在尋找一個內部支撐較少的角度上。
2e. 金屬3D列印時的成本考量
從金屬3D列印時的成本考慮,這一頁的詳細討論將在後續的主題中展開。
2f. 綜合考慮不同因素
綜合上述不同因素,需要得出一個綜合考慮角度和內部支撐的最佳擺放角度。這樣的擺放結果和考量將在確定角度時詳細考慮。
當我們實際考察增材製造過程中零件的定位方式時,可以發現零件的放置角度對於其金屬3D列印效果和質量有著重大影響。不同的放置方式,如豎放、橫放、或斜放,對零件的性能和金屬3D列印效率會產生不同的影響:
-
豎着金屬3D列印:在這種方式下,零件的XY平面截面很小,因此承受的壓力不特別大。但是,零件放置得越高,金屬3D列印所需的時間就越長,且金屬3D列印過程中出錯的概率也會相應提高。
-
橫着金屬3D列印:當零件在XY平面上橫放時,其橫截面會變大,從而承受的壓力也會顯著增加,這可能導致零件容易發生翹曲現象。
-
斜着金屬3D列印:斜放的零件會出現階梯紋理,這是因為層厚和金屬3D列印角度導致部分切片細節丟失。
最佳的零件定位考慮了不同因素的綜合影響,給出一個綜合考慮的擺放建議。如節點2f所述,考慮的因素包括內部支撐的重要性、支撐和時間的次要考慮,而金屬3D列印時的空間範圍不作為主要考量。隨着這些擺放因素重要性的變化,最佳的零件定位也可能需要進行調整,這一點在後續的如圏4所示將進一步展開。
理想中,擺放零件時需要綜合考慮多個因素,以確定最佳的擺放方案。在實際操作過程中,通常會優先考慮某些關鍵因素,例如內部支撐的需求,然後根據這些初步的擺放結果,再根據其他因素進行調整。這種方法反映了在確定最佳擺放位置時各因素重要性的權衡。一個典型的實務操作流程是,工程師在獲得零件後,首先檢查零件哪些部位添加的支撐難以移除,在避開這些角度後,形成一個大概的擺放方向,隨後考慮支撐的數量、刮刀方向、金屬3D列印時間等因素,最終確定擺放角度。
零件的擺放是增材製造數據準備階段首先遇到的問題。在進行擺放時,不僅要考慮如何添加支撐,避免與刮刀碰撞,還要關注對表面金屬3D列印效果的影響。顯然,擺放對於金屬3D列印的數量、時間等也有所影響。這就是為什麼在增材製造設計初期,我們需要先討論擺放問題。
在考慮擺放時,需要關注零件的不同特徵,其中零件相對於金屬3D列印平台的角度是一個重要的考量因素。以立體零件為例,可以將零件表面根據功能和形態劃分為不同的區域,並用不同的顏色表示:
- 淺藍色表示上表面區域。
- 黃色表示下表面區域。
- 紅色表示側垂面區域。
- 粉色表示階梯面區域。
- 灰色表示垂直壁面區域。
這種顏色劃分有助於在設計和準備階段更好地視覺化和理解零件的不同面向和相關的擺放需求,進而制定出更加合理和優化的增材製造方案。
這種劃分揭示了零件的不同特徵區域,顯示出一些區域之間存在重疊,例如階梯區域既可以出現在上表面,也可能出現在下表面;部分下表面區域還可能包含側垂區域等。這樣的不同區域劃分是基於其與水平面的相對角度進行的判斷。具體到圖6中的詳細解釋,零件被藍線和紅線所圍繞的區域,其中紅線代表了某一特徵區域,該區域朝下,表示為下表面區域。上方的藍線與水平面大致平行,紅線與藍線形成一個夾角�a。根據實際情況,不同區域的劃分界限角度可以進行調整,如果按照圖6b的設置,則:
-
夾角a小於20°:這樣的區域被劃分為下表面區域,通常會產生階梯效果,需要添加支撐以保證金屬3D列印時的穩定性和精確度。這些區域以粉色表示,指出這些區域在打印過程中的特別處理需求。
-
夾角a在20°到45°之間:這些區域通常需要添加支撐,以防止金屬3D列印過程中的結構失穩或是質量問題。這些區域以紅色表示,標示出需要特別注意支撐問題的特徵區域。
-
夾角a在45°到60°之間:這些區域的處理需要根據零件結構、使用的材料以及補粉角度等因素綜合考慮,以決定是否需要添加支撐。以黃色表示,這顯示了這些區域在設計和金屬3D列印過程中可能需要更加靈活的處理方式。
-
夾角a大於60°:這些區域通常不需要添加支撐,因為夾角較大,零件的這些部分能夠在無需額外支撐的情況下穩定金屬3D列印。這些區域以灰色表示,指示出這些區域在金屬3D列印過程中相對較為簡單處理。
這種對零件特徵區域的細分和顏色標示,不僅有助於設計階段對零件進行詳細分析,也便於在金屬3D列印準備過程中針對不同區域採取適當的支撐策略,從而提高金屬3D列印效率和零件質量。
在增材製造過程中,添加支撐的一個關鍵參數是垂直角度,亦即自支撐角度。通常情況下,這個角度被設定為45°。然而,在實際應用中,這一角度可能會因材料、刮刀方向、層厚度、以及預熱溫度的不同而有所調整。對於設計師來說,在進行零件設計時,必須綜合考慮零件的朝向、垂直角度以及階梯效果角度。一旦確定了零件的最佳擺放方式,就可以進行針對性的設計優化,例如:
-
面對具有特定角度的結構:應儘量避免角度小於45°的設計,以減少需要添加支撐的情況。這裡的基本原則涵蓋了空間(如圖9a所示)、角度(如圖9b所示)以及水平孔洞(如圖9c所示),這些示意圖清晰地指出了哪些情況下需要加入支撐。
-
減少低於20°的角度設計:以避免產生階梯效應,這樣的設計原則有助於提高零件的表面質量,並減少後續的加工處理。
2.設計規則
每種加工技術都有其獨特的設計原則,金屬3D列印亦然。過往章節提及的過角度、擺放及支撐等,均為設計過程中必須細心考量的要素,特別是在金屬增材製造中,支撐的設計至關重要。
在設計零件時,我們不僅需關注支撐結構本身,更要全面考慮支撐對零件整體品質的影響。透過結構設計的優化,既可以調節支撐的強度,也能在可能的情況下減少支撐的使用。本節將詳細介紹添加支撐的關鍵準則及在設計時需注意的結構細節。
2.1懸空
在增材製造特別是粉末床熔融技術中,需要特別關注的一類結構是過懸空結構。過懸空結構如果沒有適當的支撐,可能會因為已成型部分產生的殘留應力和下方粉末無法充分支撐上部組件而導致零件變形。添加支撐的目的就是為了解決這些過程中的問題,保證過懸空結構的可金屬3D列印性。
以下是不同過懸空量對金屬3D列印結果的影響(以不銹鋼為例):
-
當過懸空量小於1mm時,結構可以不添加支撐而直接金屬3D列印,且能保持良好的形狀。
-
當過懸空量大於1mm時,則需添加支撐。在實例中,1mm的過懸空結構雖然可以金屬3D列印出來,但其下表面會出現一定程度的不規則區域。
-
對於2mm的過懸空結構,如果不添加支撐,則無法成功金屬3D列印,或會出現明顯的塌陷現象。
通過添加支撐,即使是較大的過懸空結構也能被成功金屬3D列印。在設計支撐時,可以考慮不同類型的結構設計,如實例中展示的低懸空結構支撐、傾斜支撐和實體支撐等。
在進行金屬3D列印時,對於過懸空結構的一個基本考量是其過懸空量通常定義為1mm。需要注意的是,相同結構在不同的擺放角度下,其對過懸空區域的支撐需求也會有所不同。
2.2金屬3D列印角度
關於金屬3D列印的規則關注於角度。經驗法則指出,當特征的水平方向夾角大於45°時,則不需要添加支撐。不過,這一規則可能會根據不同的材料或是不同的金屬3D列印機有所變化。
特征角度是指零件元素不需支撐即可加工的最小夾角。通常情況下,使用大於最小角度的角度,可以製造出表面質量更好的零件。這是因為朝下的表面通常比朝上的表面擁有較差的表面質量。當表面朝下的程度增加(越接近水平),表面質量就越差。在能量束聚焦處熔化材料後迅速冷卻,產生的皮膚力會使材料向上卷曲。而支撐則作為零件與成型平台之間的「橋樑」,用來抵抗這種向上的翹曲力。過度翹曲的區域可能會阻礙新一層的粉末正常鋪展,甚至可能卡住或損壞刮刀,超過一定程度的翹曲甚至可能導致金屬3D列印失敗。
直接在粉末床上打印零件,若不使用支撐作為熱量分散的橋梁,可能會導致零件表面質量變差。這是因為當激光掃描粉末床上的粉末時,疏松未熔化的粉末會因受熱而聚集並粘接在剛掃描未完全冷卻的零件表面上。缺乏支撐結構及時散發熱量,導致熱量積累,從而引起更嚴重的粉末粘結問題。如果斜面角度設置不合理,也會使零件的表面質量變差,嚴重時甚至可能損壞補粉裝置。
2.3 細柱狀與薄壁
對於薄壁結構或細棒等細長結構,在打印過程中容易出現問題。如果較大面積的薄壁結構沒有在設計上加強,那麼在打印時很容易發生變形。從薄壁的壁厚或細棒的粗細來看,使用常規激光器打印時,最薄(最細)的結構大約是0.2mm。通過調整打印工藝,這個尺寸可以降低到約0.15mm左右。如果使用小光斑激光器,厚度甚至可以低於0.1mm。
此外,類似細棒型結構的穩定性還與其長度(長細比)相關。例如,直徑為1mm的細棒,在高度約8mm左右時,打印可以無異常,但如果想打印更高的結構,則可能在打印過程中發生變形。不同材料和打印設定,其允許的最大長細比也有所不同,一般認為長寬(長細)比大於8時,零件容易發生明顯變形。
2.4列印間細距
在3D打印過程中,激光作為主要的加工「刀具」,其工作時的直徑為80微米。然而,考慮到熱影響區域的擴展,其有效直徑可能擴大到150微米至250微米。這一擴展受到原材料特性的影響,導致打印形成的結構邊緣會有粘連的粉末。此外,由於打印是一個熱過程,整個結構會在不同方向上產生收縮。結合這兩個因素,金屬3D打印能夠成型的最小間隙是有限制的。
如案例所示,最小的垂直孔徑約為0.4mm,最小縫隙也為0.4mm。隨著測試件高度的增加,可以觀察到0.4mm的垂直孔有輕微的「擠壓」現象,即孔徑變小,這是由於之前提到的在熱過程中產生的收縮所導致的。
打印的零件周圍被半燒結狀態的粉末包圍,因此需要預留足夠的空間進行噴砂(或其他後處理)以清理零件的縫隙和圓孔中殘留的粉末。對於較大的零件,這意味著需要預留更大的空間以便於將粉末徹底清除。一般而言,1mm的間隙足以對成型平台上的零件進行有效的熱隔離,但水平方向的槽寬和圓孔直徑的具體尺寸需要根據打印設定和材料的特性來確定,因為這些數值與打印參數、材料的相容性關係密切。同時,為了防止打印過程中出現應力集中,建議在內部的尖角處進行倒角處理。
2.5 懸空和孔
懸空結構是由兩個或多個特徵支撐,且底面平整朝下的結構。這些結構實際上是懸空設計準則的拓展,與之前提到的單懸空結構相比,懸空結構可以容納更大的「懸空」。
懸空結構的測試顯示:
- 1mm的懸空結構:沒有顯示明顯的異常。
- 2-4mm的懸空結構:可以看到一些變形。
- 5-6mm的懸空結構:下表面變形較多,但1-6mm的懸空結構仍可以成功打印。
水平圓孔的測試顯示:
- 4-7mm的圓孔:沒有顯示明顯的異常。
- 8mm的圓孔:出現了細小的下表面變形。
- 9-10mm水平孔:下表面變形區域進一步擴大。
這些觀察結果強調了,在進行增材製造設計時,充分考慮結構的尺寸和形狀對於確保打印質量和零件穩定性的重要性。透過適當的設計調整和參數選擇,可以有效地優化打印結果,減少變形並提高零件的整體性能。
2.6 尖角
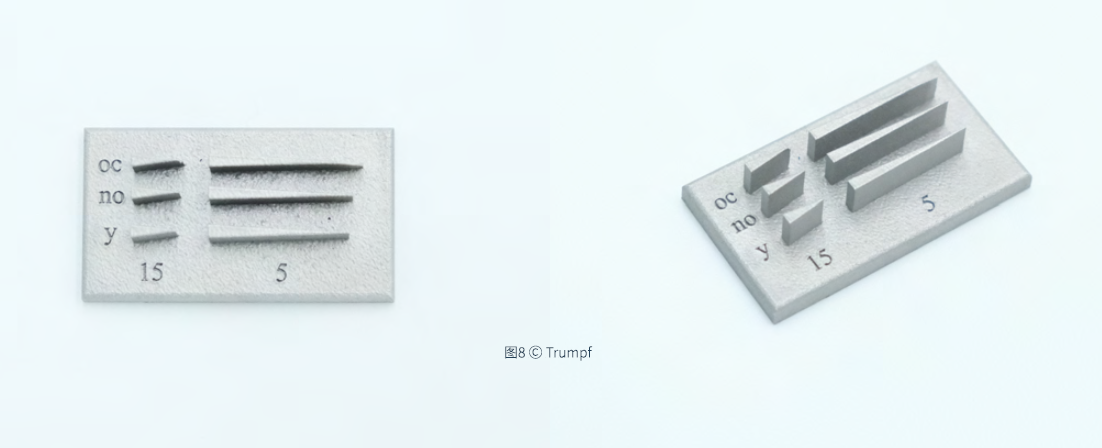
在尖角結構的3D打印過程中,由於光斑偏移的影響,其輪廓線往往會向內部收縮,導致部分結構無法被精確打印出來或是細節丟失。不同角度的尖角示例顯示,如果在打印時不使用額外的尖角優化措施,其尖角細節可能部分丟失,尖角變得略為鈍化。
3. 結構優化
對於金屬3D打印,前期的支撐設計是一個重要的步驟,需要經驗豐富的工程師進行。打印時支撐結構會消耗額外的原材料和時間,後處理時還需進行支撐去除工作,這可能會導致表面質量下降,甚至損壞零件。在零件設計中,通過對某些結構進行優化,可以減少對支撐的需求。本章節將介紹常見的結構優化方法。
3.1 懸空
對於懸空結構的優化,可以採用以下三種倒角方法來將懸空結構修改成可以自支撐的結構:
- Chamfer(直角倒角):透過將尖銳的直角轉變為斜面,來減少懸空結構的直接支撐需求。
- Convex radius(凸型圓角):將角落處改為凸出的圓角形狀,增加結構的自支撐能力。
- Concave radius(凹型圓角):通過在角落處設計凹入的圓角,以改善懸空的支撐情況。
透過這些優化措施,可以在不影響零件功能和美觀的前提下,有效減輕後續支撐去除的難度和提升零件的整體打印質量。
比較不同圓角結構打印後的表面狀況,我們可以觀察到:
- 凸型或凹形圓角:對於懸空結構的打印有所幫助,但在其下方的粉末輪廓可能存在缺失,表現為過度燒結或未熔化的情況。
- 直角倒角:則展現出較好的下表面質量。
在優化懸空結構時,不同的倒角方法都能確保打印正常進行。如果對結構的完整性和表面質量有較高要求,推薦使用直角倒角進行結構優化;而在後期需要進行相應的後處理來去除添加的倒角時,三種角度的倒角方法均可選擇使用。這樣的優化不僅提升了打印效果,也為後續處理提供了更多的靈活性。
3.1 孔的狀形
在3D打印過程中,特別是對於直徑大於8mm的水平孔,建議添加支撐以確保打印質量。在添加支撐的同時,需要特別考慮到支撐的去除工作,因為從零件內部去除支撐往往比從外部更加困難。對於有曲線或彎曲的管道結構,從內部去除支撐尤其具有挑戰性。
對於孔的形狀優化,可以通過縮小孔徑或調整孔的結構來實現。將孔徑降低到8mm以下可以避免需要添加過多的支撐。對於孔的結構優化,推薦以下幾種設計:
-
沮滴形孔:沮滴形孔可以實現幾乎任何尺寸的打印,只要預留角度不小於最小自支撐角度。一般做法是將沮滴形孔的頂部切割成圓角,以避免應力集中。
-
橢圓形孔:當其長軸位於Z方向,且頂部是圓弧形狀時,橢圓形孔在高度是寬度的兩倍時,可以將橢圓孔的高度打印到約25mm。
-
菱形孔:頂部結構類似於沮滴形孔,菱形孔幾乎可以打印成任何尺寸。建議對孔內的角進行倒角處理,以避免應力集中。
這些優化設計不僅能夠提高零件的打印質量和穩定性,還能夠在後處理階段減輕去除支撐的難度,進一步提升整體製造效率。
3.3 邊緣收縮
圖14展示的邊緣收縮現象,這種現象經常發生在零件截面變化的區域。在截面變化的區域,每層新增的材料都會收縮,導致結構向固定端收縮。隨著打印過程的進行,會出現不一致的收縮。從結構設計的角度考慮,處理這一問題的方法通常有:
-
對結構進行優化,減少大截面積的面積。如圖15所示的格柵零件,中間需要有縫隙,原始設計為最右端的零件。調整不同的內部結構後,靠近右邊第二個設計在頂部的變形最小。這是因為其中頂部小圓孔設計的引入,減少了頂部的截面面積,減弱了收縮時的力量,從而減少邊緣收縮。
-
對可能出現收縮的區域額外添加材料,之後利用後處理去除。如圖16所示,在零件左側預測會出現收縮的區域額外添加了材料,作為對比,右側沒有做材料添加。打印後,利用打磨或其他後處理方式,去除多餘的材料。
在探討金屬3D打印過程中的設計優化和支撐策略時,我們了解到懸空結構、孔的形狀、尖角以及邊緣收縮等都是關鍵考量因素。透過針對這些特定的挑戰採取適當的設計調整和支撐策略,可以顯著提高打印效率、降低後處理工作量並提升零件質量。
結構的優化不僅涉及減少必要的支撐結構,還包括對零件形狀和內部結構的細微調整,以適應金屬3D打印的特性。這包括但不限於利用倒角、調整孔徑、以及改變結構截面,以減輕打印過程中的應力集中和材料收縮對終產品質量的影響。
最後,隨著增材製造技術的不斷進步和成熟,對於設計師和工程師來說,了解和應用這些優化策略將越來越重要。這不僅能夠提升設計的實現可能性,還能夠確保製造過程的高效與經濟性,同時滿足日益嚴格的性能要求。透過持續的學習和創新,我們可以不斷推進金屬3D打印技術的發展,拓展其在各行各業的應用前景。